Our COVID-Economy Story
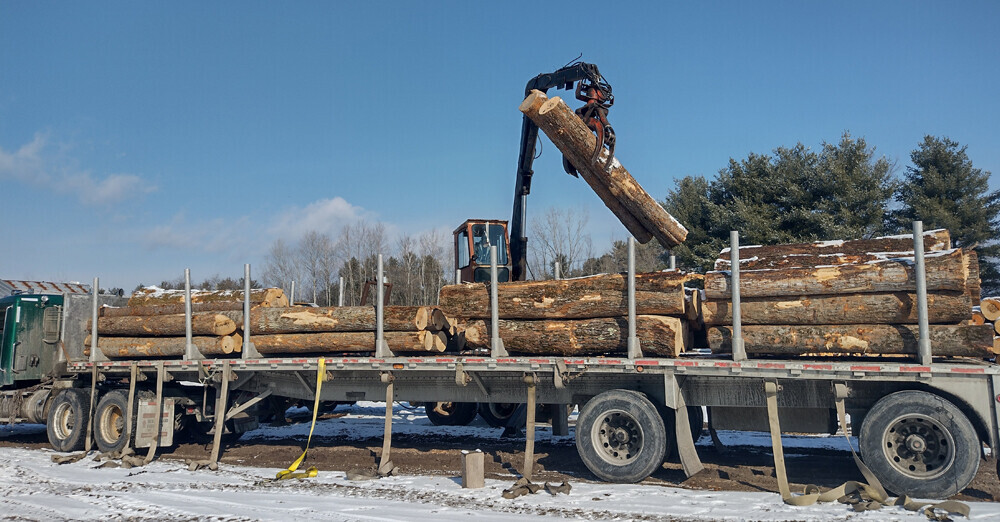
All of us in business have been stressed over the last couple of years, dealing with supply chains, transportation, product shortages, higher prices, and workforce challenges. The balance of all these issues is a little different depending on the details of the enterprise.
Last year, a retailer asked us how we could be having difficulties filling orders, “I thought you made everything in the US, not like the companies whose products are waiting on ships.” Well, yeah but…
What we are all going through is a learning experience in how tightly synchronized our economy operates during “normal times”. Now is not normal. It isn’t just ocean freight or baby formula, it is an entire economy thrown out of sync, which leads to delays and greater costs in getting anything done. When things are going well, you can know how much something will cost and how long it will take. There is capacity to adjust to reasonable changes along the way. Transacting business favors certainty and stability. Customers can anticipate costs and lead times. Manufacturers have trusted sources for acquiring their inputs. All this does not describe an inherent societal structure and we should appreciate the competence and effort behind a system when it works right. We should also appreciate how little it takes to get thrown off course.
As a manufacturer, a lot of operational certainty has eroded. For example, a machine repair part that used to arrive in 24-48 hours now takes 1-2 weeks and production is either delayed or finds a less efficient Plan B. Lumber is taking a wild ride and we have to stock more just to have it. Do not equate the headlines about building material prices to our material prices, it is not the same. There is one connection, lots of pine has been diverted to construction, so the elevated price of pine lumber is now higher than the elevated price of maple.
Workforce is a major problem in our region, running 2.5% unemployment. Maple Landmark usually has a stable staff, but we’ve been around a long time and have experienced a lot of retirements in recent years. Finding replacements and covering growth needs is a challenge. The complexity of our product lines means a long learning curve.
So, our bottom line is that, considering all these conditions and despite our lumber supply chain being mostly within 30 miles, there are a lot of stumbling blocks to deal with. We have been able to maintain a great crew who have weathered the early-COVID shutdowns and the overwhelming demand as things opened back up last year. Some (normal) years, to make it through the holiday season, we’ve had to dust off special tracking systems for a few weeks to handle order backlogs. Now, we’ve employed that tactic since August 2021. The lists are short right now, but our real target is to build inventory for a smoother 2022 holiday season. As the song goes, “We’ve got a long way to go and a short time to get there.”
Price Increases
As you are seeing, cost increases are happening everywhere around us. Materials cost more, people need more to live on, and operational bumps lead to costly inefficiencies. We held back last year and kept increases modest, hoping some of the elevated costs we were seeing were short term. Instead, everything keeps going up. We looked to sharpening our pencil but after decades of competing for business against imports, the pencil has always been kept really sharp. The reality is that, whether stuff is domestic or imported, there is no escaping price increases.
About that sharp pencil, you’ve probably noticed more of our product that has been laser cut. We bought new laser equipment last year that has led to both new products and changes in process for some existing products. The newfound flexibility has been the highlight of the past year. The main benefits are more design options, labor savings, and improved lumber yield (cutting fewer trees). This is very expensive equipment to purchase and maintain, so most of the savings cancel out, and the benefit is getting product made without having to hire more people (who don’t seem to exist).
We remain dedicated to domestic production, and we are non-stop in our efforts at continuous improvement, to provide you with interesting products, at a good value, and in a timely fashion.